A futuristic element common in helicopter production makes a key difference.
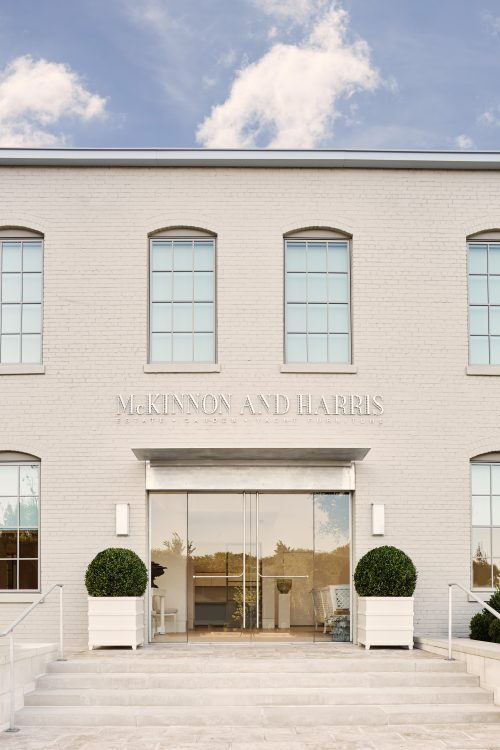
The exterior of McKinnon and Harris’s Richmond workshop has been landscaped under cofounder Will Massie’s instruction.
Step inside the airy, elegant showroom of McKinnon and Harris’s Richmond HQ—double height ceilings, soaring indoor trees, and collected antiquities surrounding the brand’s elegant outdoor furniture—and you might not have any idea what kind of magic is really brewing behind the scenes. Past the company’s offices and showroom is something of an artist’s studio meets mad scientist’s lab. Here, expert artisans train for up to five years to perfect their skills working with the company’s aluminum frames—topped with a “secret sauce” borrowed from the marine and aeronautics industries.
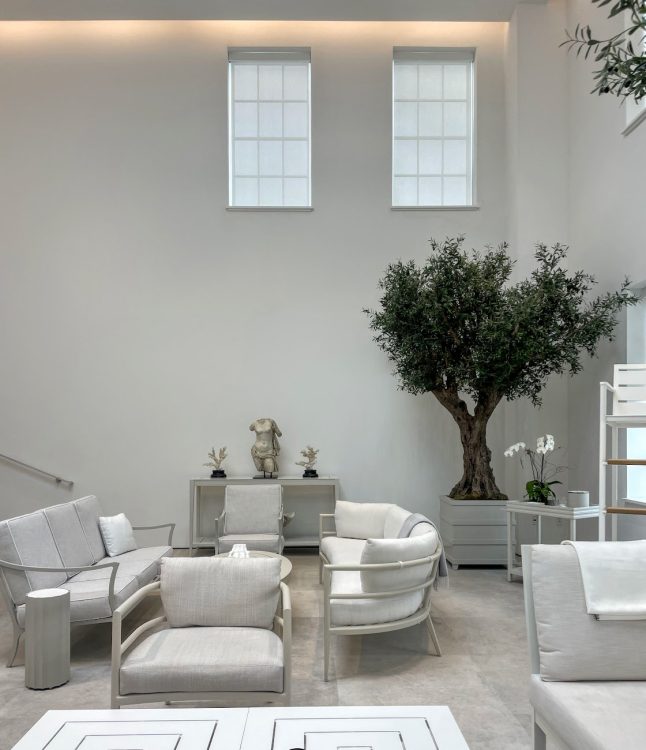
Image courtesy of Hadley Keller
The process behind each McKinnon and Harris piece is painstakingly exact, beginning with slabs of raw aluminum. These pieces are cut, shaped, and welded together to form a rough frame, which is then sent to a series of “sculpting” stations, where artisans carefully smooth over each weld with a variety of sanders, developing graceful curves and clean edges where welding left lumpy metal. Artisans here work for two years to learn the skills of sculpting—it takes five to fully master the step.
“Since aluminum is prone to corrosion, we developed a way to prevent even the smallest bubble.”
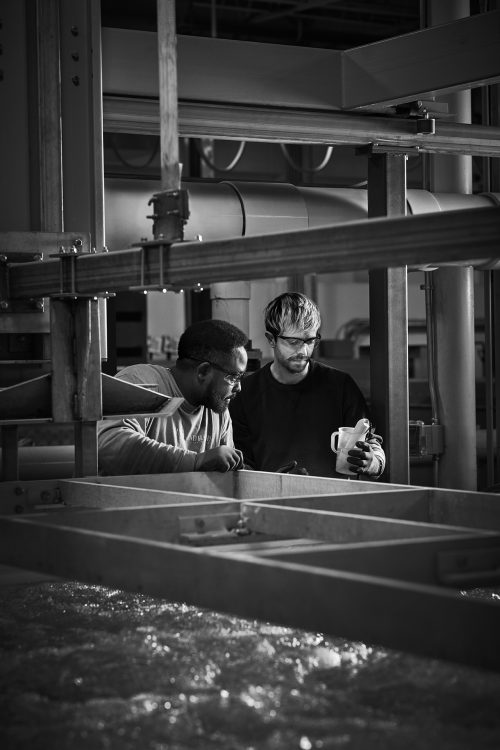
Image courtesy of McKinnon & Harris
Once the frames are smoothed and checked for quality, they are lined up outside a closely-monitored room where a constant whirring sound obscures background noise. Inside are 12 pool-sized dunk tanks of water, which the furniture progresses through, washing and thoroughly rinsing up to the final tank, where the process sharply differs from many other manufacturers.
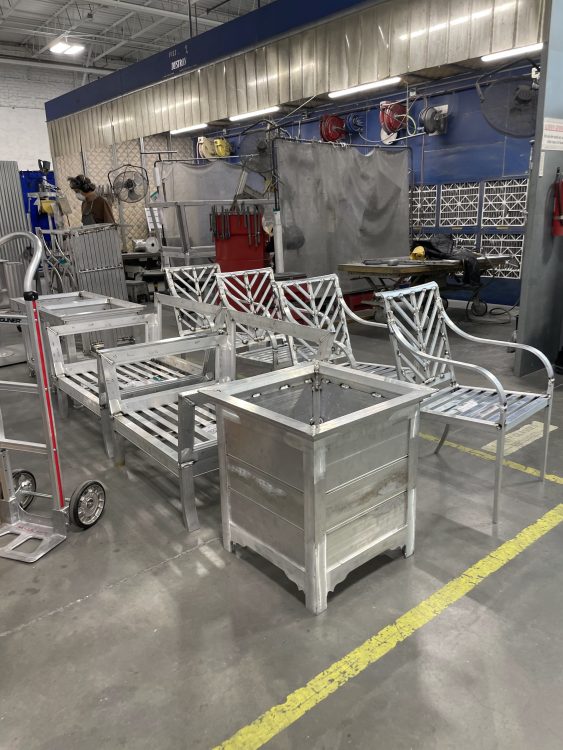
Image courtesy of Hadley Keller
The eighth tank is “where the magic happens,” as the McKinnon and Harris team says. This magic is borrowed from the nautical and aerospace industries where any bit of corrosion can become life-threatening. Since aluminum is prone to corrosion, manufacturers had to find a way to prevent even the smallest bubble of reaction on the surface of the metal to ensure its longevity for use in commercial, industrial, and military-grade settings. That’s where this final tank comes in.
Following its wash cycle, McKinnon and Harris furniture is placed into a titanium solution, then charged with a shocking two megawatts of electricity—a process that causes the metal to literally glow. Afterwards, the surface, now a dark charcoal gray, is impenetrable to corrosion. Though this process is familiar in technical and military manufacturers, McKinnon and Harris’s facility represents its only use in the home design arena. With this base in place, the furniture receives a coat of adhesive primer, followed by a powder coating, sealing the metal without the possibility of corrosion forming inside. Suffice it to say, those outdoor tables won’t have any problem in a rainstorm.
If you’re interested in visiting McKinnon and Harris’s Richmond headquarters yourself, contact hadley@designleadershipnetwork.org.